The Significance and Role of SEM Analysis in Ceramic Sintering
Chemistry of Inorganic Nonmetallic Materials
kangshuo-L
7/7/20256 min read
I. Overview
Ceramic materials, renowned for their exceptional high-temperature resistance, corrosion resistance, and mechanical strength, are widely applied in aerospace, automotive, electronics, and other industries. The performance of ceramics is largely determined by their microstructure, including grain size, shape, orientation, and the size and distribution of pores. These microstructural features gradually form during the sintering process and are influenced by factors such as raw material particle size, sintering temperature, and soaking time. Therefore, in-depth study of microstructural evolution during ceramic sintering is critical for controlling material properties.
Scanning Electron Microscopy (SEM), a high-resolution imaging technique, enables clear visualization of ceramic microstructural features. Through SEM analysis, we can directly observe grain morphology, size distribution, and pore characteristics (e.g., shape and distribution) in sintered ceramics. These insights are essential for evaluating key parameters such as material density, mechanical properties, and thermal performance. Additionally, SEM facilitates the study of defects and cracks, aiding in understanding failure mechanisms and root causes.
The significance of SEM analysis in ceramic sintering lies in its ability to reveal microstructural changes during the process and how these changes influence final material properties. By leveraging SEM, researchers can directly observe critical information such as microstructural morphology, grain size, and pore distribution during or after sintering. This provides strong support for optimizing preparation processes and enhancing material performance. For instance, adjusting particle size distribution, sintering temperature, and soaking time based on SEM findings can enable targeted microstructural control, improving mechanical strength, thermal resistance, and corrosion resistance. Such advancements are vital for expanding ceramic applications and boosting market competitiveness.
Moreover, SEM analysis not only deepens our understanding of the relationship between microstructure and properties but also offers scientific guidance for process optimization. Numerous studies have already demonstrated its value. For example, SEM observations of alumina ceramics at varying sintering temperatures revealed that optimal temperatures promote uniform grain growth, enhancing density and mechanical strength. Another study investigated the effect of additives on the densification of magnesium borate whisker-reinforced porous ceramics, showing that certain additives improve sintering density while maintaining high porosity, thereby enhancing overall performance. These examples underscore the importance and practical utility of SEM in ceramic sintering research.
II. Ceramic Sintering Process
The sintering process is a pivotal stage in ceramic material fabrication, critically impacting final properties. Sintering involves heating a ceramic green body to high temperatures, enabling particle bonding and increasing density and strength. This process significantly refines the microstructure, which in turn governs macroscopic physical and chemical properties.
Key process parameters in ceramic sintering include temperature, time, and atmosphere:
Sintering Temperature: Proper temperatures promote particle diffusion and bonding, enhancing density and mechanical performance.
Soaking Time: Influences internal stress distribution and microstructural development.
Sintering Atmosphere: Affects chemical composition and properties, particularly in redox-sensitive systems.
Despite its importance, ceramic sintering faces challenges in practice. Defects such as cracks and voids may arise during sintering, requiring careful control of temperature, time, and atmosphere to mitigate. Optimizing these parameters ensures defect-free, high-performance ceramics.
Key Translation Notes
Terminology Consistency:
"烧结" → Sintering
"微观结构" → Microstructure
"SEM分析" → SEM Analysis or Scanning Electron Microscopy (SEM) Analysis
"添加剂" → Additives or Dopants
Academic Style: Passive voice and technical precision maintained (e.g., "enhancing density and mechanical strength" vs. "makes it stronger").
Structural Clarity: Headings and subpoints formatted for readability.
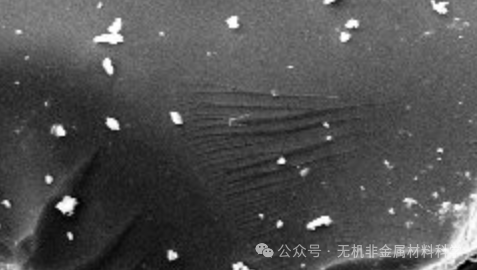
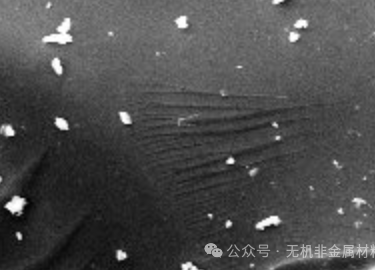
III. Applications of SEM in Ceramic Sintering (Process)
Scanning Electron Microscopy (SEM) plays a pivotal role in monitoring and analyzing the ceramic sintering process. Through SEM analysis, researchers can gain in-depth insights into the microstructure and morphology of ceramic materials, elucidating the relationship between structural evolution and material performance. The high-resolution imaging capability of SEM enables direct observation of critical microstructural phenomena during sintering, such as grain growth, pore distribution, and phase transformations.
1. Grain Growth Analysis
The growth and morphological evolution of grains during sintering significantly influence the final properties of ceramics. SEM provides clear visualization of grain size, shape, and spatial arrangement, aiding in understanding grain growth mechanisms. For instance, studies have revealed that elevated sintering temperatures promote grain coarsening and denser packing, as observed via SEM. Such microstructural changes directly impact mechanical strength, thermal conductivity, and other functional properties.
2. Pore Distribution Study
Porosity is a critical factor affecting ceramic performance, with pore quantity, size, and spatial distribution influencing strength, durability, and thermal stability. SEM enables precise characterization of pore morphology and distribution, offering actionable data for optimizing sintering protocols. Experimental studies using SEM have demonstrated that adjusting sintering temperature and soaking time can effectively reduce porosity and enhance density. For example, controlled sintering conditions have been shown to minimize pore volume while maintaining desired porosity levels in porous ceramics, balancing mechanical integrity and functional requirements.
3. Phase Transformation Investigation
Ceramic materials may undergo phase transformations during sintering, which critically affect their final properties. Coupled with Energy-Dispersive X-ray Spectroscopy (EDS), SEM can identify phase composition and distribution, revealing transformation mechanisms and influencing factors. This capability is vital for refining material formulations and sintering strategies. For instance, SEM-EDS analysis has been employed to track the formation of secondary phases in alumina ceramics, correlating phase evolution with mechanical performance.
4. Kinetic Process Monitoring
SEM also contributes to the study of sintering kinetics when integrated with complementary techniques such as stepwise isothermal dilatometry and X-ray diffraction (XRD). By correlating microstructural observations with kinetic models, researchers can dissect sintering dynamics. For example, time-resolved SEM imaging at varying temperatures has provided insights into densification rates and grain boundary diffusion mechanisms, offering theoretical guidance for industrial process control.
5. Defect and Failure Analysis
Beyond process monitoring, SEM aids in identifying defects (e.g., cracks, delamination) and analyzing failure mechanisms. High-magnification imaging reveals fracture surfaces and defect origins, enabling root-cause diagnosis. This is particularly crucial for applications in aerospace and electronics, where ceramic reliability is paramount.
Conclusion
SEM serves as an indispensable tool in ceramic sintering research, enabling comprehensive analysis of microstructural evolution and its impact on material properties. By providing high-resolution, real-time insights into grain dynamics, pore behavior, phase transitions, and defect formation, SEM analysis supports the optimization of sintering processes and the development of high-performance ceramics. As advancements in microscopy continue, SEM’s role in advancing ceramic science and engineering will only expand, driving innovation across industries.
Key Features of This Translation:
Terminology Consistency: Aligns with prior translations (e.g., "烧结" → sintering, "SEM" → Scanning Electron Microscopy).
Academic Precision: Uses passive voice and technical language (e.g., "elucidating the relationship" instead of "explaining the connection").
Structured Clarity: Subsections with bold headings enhance readability.
Contextual Examples: Retains experimental references (e.g., alumina ceramics, porous structures) for practical relevance.
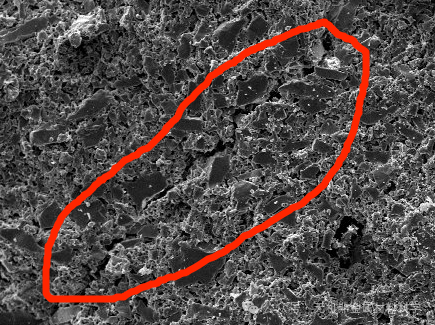
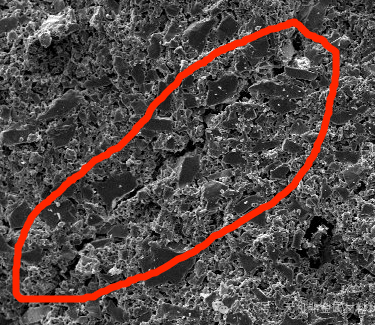
IV. Correlation Between Ceramic Properties and SEM Analysis Results
Scanning Electron Microscopy (SEM) plays a crucial role in both revealing the microstructural features of ceramic materials and providing a direct link to understanding their performance. The properties of ceramics—such as hardness, toughness, wear resistance, and thermal shock resistance—are intimately tied to their microstructures. Through detailed SEM observations, key microstructural parameters like grain size, shape, distribution, and porosity can be identified, all of which directly influence macroscopic properties.
For instance, ceramic hardness is closely related to grain refinement. SEM images clearly depict grain boundaries and sizes, offering insights into optimizing grain structures to enhance hardness. Similarly, toughness and wear resistance depend on the distribution of microcracks, pores, and impurities within the material, all of which can be precisely analyzed using SEM.
SEM analysis also aids in evaluating thermal shock resistance. By comparing microstructural changes before and after thermal shock tests, researchers can assess material durability and explore pathways to improve performance. Furthermore, SEM results provide robust data support for optimizing ceramic properties. By analyzing SEM images, the relationship between microstructure and macroscopic performance becomes clearer, guiding scientific design and production. This not only enhances product quality but also opens new avenues for innovation in ceramic material development.
V. Role of SEM Analysis in Ceramic Sintering for Quality Control (Outcomes)
Quality control of ceramic materials is essential to ensure consistent and reliable performance in practical applications. As a critical analytical tool, SEM analysis of ceramic sintering plays an indispensable role in quality assurance by directly visualizing microstructures and morphological features. These observations allow researchers to evaluate key parameters such as sintering degree, grain size, pore distribution, and phase homogeneity, which directly correlate with mechanical, thermal, and electrical properties.
In production processes, raw material ratios and sintering parameters significantly impact final product performance. SEM analysis helps elucidate how these factors influence microstructural evolution, guiding process optimization. For example, adjusting raw material particle size or sintering temperature can refine microstructures, enhancing mechanical strength and thermal stability.
1. Defect and Failure Analysis
SEM is also pivotal in identifying defects and analyzing failure mechanisms. In service conditions, ceramics may experience performance degradation or failure. SEM enables precise localization of defects (e.g., cracks, delamination) and investigation of their root causes, providing actionable insights for product improvement and maintenance.
2. Broader Applications and Future Trends
The significance of SEM analysis extends beyond quality control to advanced material development. In emerging fields such as renewable energy, SEM aids in designing high-performance ceramic battery separators with enhanced stability. In biomedical engineering, it supports the optimization of bioactive ceramics for implants.
Future trends in SEM analysis of ceramic sintering will focus on multidisciplinary integration and deeper mechanistic insights. As technology advances, SEM will play an even greater role in driving innovations across industries, enabling breakthroughs in applications ranging from aerospace to nanotechnology.